Migiwa Imaishi
Researcher, Independent Administrative Institution National Institutes for Cultural Heritage Tokyo National Research Institute for Cultural Properties
The history of ships in the Japanese archipelago begins with rafts and logboats (hollowed boats), which developed into semi-built-up ships made by connecting planks to a hull, and further into built-up ships made solely of planks. Strong aspirations for larger ships and advancements in lumbering and shipbuilding techniques made it possible for this gradual development. However, it was in no way a linear development.
Throughout the archipelago, ships of various forms and in different stages of this evolutionary development were in use alongside each other until recently. Small wooden boats that were used for inshore fishing, in particular, displayed regional characteristics and took on diverse styles to match the features of each region, such as coastal topology, the roughness of the waves and currents, fishing methods and types of catches, and the availability and characteristics of natural boat materials.
Small wooden boats were mostly made by dedicated craftsmen called funadaiku (shipwright). These shipwrights differed fundamentally from homebuilders in that they needed special skills to create watertight and curvilinear constructions. Producing curves required the most experience. With logboats and some semi-built-up ships, curves were produced by gouging the wood to make dugouts, but as ships became more structured, curves construction required skills to bend the wooden planks. The most common method of bending planks involved using heat and steam. Flames and steam were directly applied to a plank while the shipwright gently bent it in the desired direction using the force of a heavy weight or vice. The bow of the boat in particular required the most advanced skills and experience as the left and rights sides had to have symmetrical twisted curves.
To increase watertightness, shipwrights used a basic procedure to press the connection of two planks closely together, such as by sawing down the joints where the two planks meet to eliminate any unevenness and evenly tapping their edges with a hammer to bring them closer together. Incidentally, with this method, the compressed parts swell by absorbing moisture, and thus make the joins even more watertight. There were also methods in which ship nails were used to connect the planks, particularly in the Seto Inland Sea area where the technique is said to have originated. A related method involves connecting planks with rivets and wooden plugs and sealing them with lacquer, as characteristically seen in the western coastal areas of Japan. Additionally, for connections with the ship’s bottom and other parts that especially required watertightness, shipwrights employed creative measures, such as beating cypress or podocarpus bark to soften it into a fabric oakum that could be packed on the inside.
These techniques and skills were rapidly lost when plastic boats became popular in the late 1960s, and the number of shipwrights also decreased dramatically. A survey on the whereabouts of shipwrights conducted by the Toba Sea-Folk Museum (Mie Prefecture) in 2002 reported the presence of roughly 170 people with shipbuilding skills (including retirees), but it is assumed that the number has further decreased over the past fifteen years. In this context, Japanese ship building techniques in the Tsugaru-kaikyo Strait and surrounding areas and the tarai-bune (tub boat) ship building techniques of Ogi, Niigata Prefecture, were designated as Important Intangible Folk Cultural Properties (Folk Techniques) in 2006 and 2007, respectively, as the first shipbuilding techniques to be so designated, in the ongoing effort to pass on the techniques to future generations.
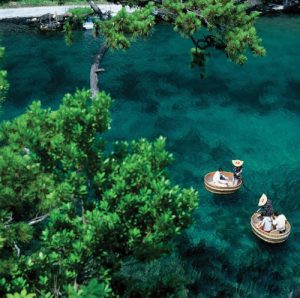
Pleasure ride on tarai-bune in Sado City, Niigata Prefecture © JNTO
The tarai-bune was invaluable to inshore fishing in the western coastal areas, such as in Niigata, Toyama, and Ishikawa prefectures, because it was able to make sharp turns in reef areas, displayed high stability, and was lightweight and inexpensive. However, it now exists only on Niigata’s Sado Island. The techniques for making taru (tubs) is similar to those applied to the boat, such that planks are connected with bamboo nails and tightened with a truss hoop to firmly fix them. However, while grained planks with excellent watertightness are used in the same manner as tubs, the tub boats incorporate additional creative measures. That is, the water-resistant heart side (the inner side of the tree) is faced inward in the case of tubs, but it faces outward in the case of tub boats. Today, the tub boats take visitors on sightseeing tours and are an important tourism resource in Sado. The city also plays a central role in holding craftsmen training courses and tub boat competitions and otherwise making efforts to promote the technical tradition and strengthen social recognition of the tub boats.